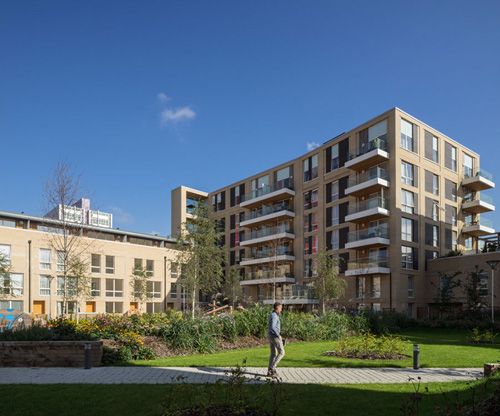
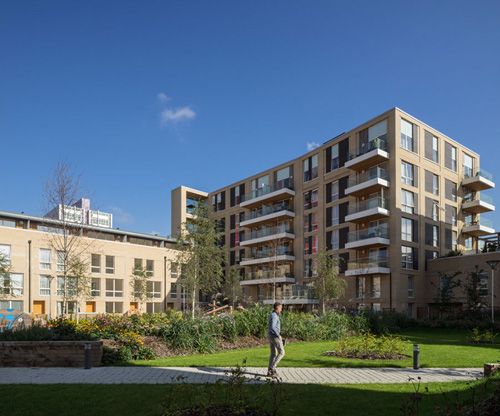
Pura Facades has seen its business grow by 34% in the last 12 months, increasing its turnover to £6 million.
Operating from West London and Birmingham, the specialist supplier of natural cladding products, works closely with architects and designers, helping them to source sustainable, safe and stylish external claddings for commercial and residential projects.
Focusing mainly on the provision of glass fibre reinforced concrete (GRC), terracotta and brick slip façade cladding panels, Pura has recently supplied several flagship projects in London, including Hallsville Quarter, a mixed use development in Canning Town, and St Mark’s Square, a major residential, retail and cinema complex in Bromley. Pura has also supplied bespoke cladding to high street outlets such as COS, Burberry and Stella McCartney.
The business attributes much of its success to the increasing appreciation of natural facades, typically using concrete, terracotta or wood, which can be eventually recycled within the construction supply chain.
Pura’s director, James Butler, said: “We founded the business four years ago to satisfy the growing demand for truly sustainable construction materials from architects and specifiers alike. The use of natural materials on new buildings has been growing over the last five years, and this is a trend that looks set to feed into other areas, such as social housing, especially as the bulk of our product range is certified as A1 non-combustible.”
Moreover, the company’s focus on customer service is another reason for Pura’s continued success. James continued: “Contractors are faced with increasingly tight delivery programmes during the construction phase and need suppliers that can help them overcome these logistical challenges. Accordingly, Pura offers contractors off-site fabrication services and timed deliveries, two methodologies that can reduce errors and improve construction site efficiencies.
“We also work hard to help contractors achieve practical completion, by providing toolbox training to site workers, giving them practical support to enable them to fill out their O&M manuals and even assisting in final snagging work. It’s these added value activities that help contractors to achieve project completion.”